You can have the most refined set of blueprints in the world, but if your equipment can’t access the site, or worse, doesn’t fit the design, you’re headed straight for a logistical mess.
Product & design synergy in construction isn’t just about aesthetics meeting mechanics. It’s about ensuring that the tools you choose work with the design, not around it.
Let’s be honest: equipment selection is often treated like a last-minute budget line. A wheel loader is a wheel loader, right?
Not quite. Ask any site foreman who’s had to squeeze one between tight scaffoldings or across unstable terrain. They’ll tell you, choosing the right construction equipment early can make or break a build.
Equipment As A Design Variable
Think about your last construction project. Did the design dictate the equipment, or did the availability of machinery restrict the design? It’s a bit of a chicken-and-egg scenario, but in reality, product & design selection should walk hand-in-hand.
Equipment like cranes, excavators, and wheel loaders doesn’t just “show up” and do the job. Their size, turning radius, fuel consumption, and operating range all affect what’s possible on a site.
A large mobile crane might need reinforced ground. A tracked excavator might chew up access paths. These are real design considerations, not afterthoughts.
On complex construction sites, ignoring this synergy often leads to retrofits, delays, and increased operational costs. Imagine ordering prefab panels that can’t be hoisted because the selected crane lacks the reach, or wasn’t even considered until midway through the project.
Where Things Fall Apart
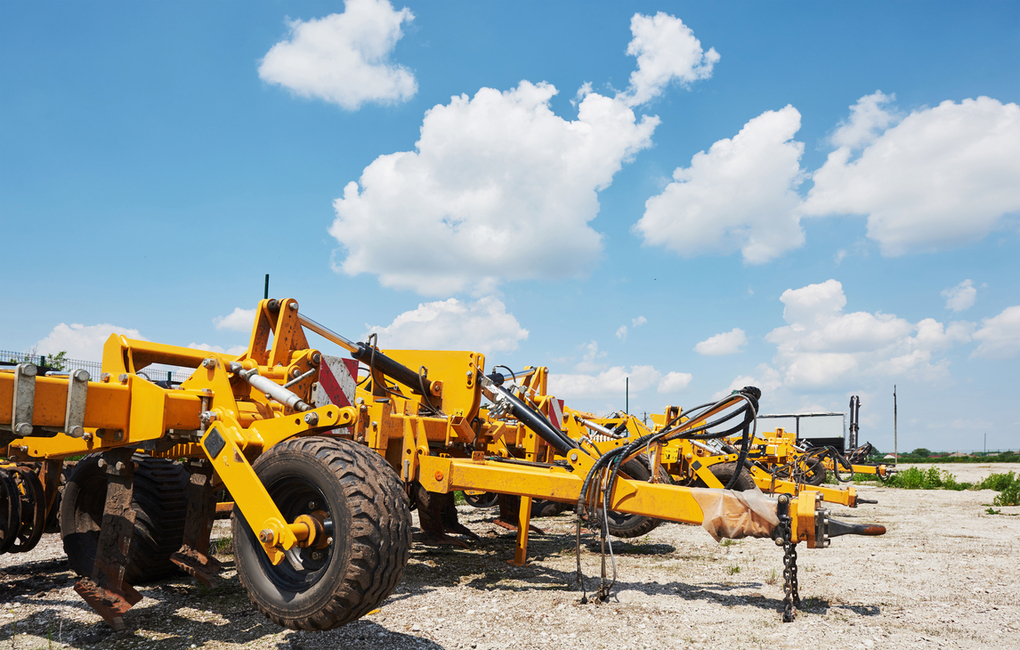
A few common breakdowns happen when construction companies treat design and equipment selection as separate conversations.
1. Late-stage procurement
By the time the plans are finalized, the equipment budget is already locked, often leaving project managers scrambling for rentals that aren’t a perfect fit.
2. Oversizing Or Undersizing
Picking heavy equipment that’s either overkill or underpowered for the job. That means more downtime, increased operational risks, or wasted fuel.
3. Siloed communication
Designers, engineers, and site supervisors are working in their corners. No cross-talk means no cross-check.
The result? A job site full of equipment that’s either hard to maneuver, inefficient, or flat-out incompatible with design features.
Making Design And Product Work Together
So, how do we fix it?
The answer lies in what good builders have always known: collaboration before concrete. Bring your equipment specialists, designers, and project leads to the same table before plans are inked and orders are placed.
Here’s how to make it stick:
Early integration
Incorporate equipment planning during design development. Not once the ink dries. A project that requires a lot of vertical material handling? Start by discussing crane options. Working on soft soil? Choose lighter gear to reduce ground compaction.
Fit-for-purpose selection
Don’t just chase brand names or raw power. Think about the actual work. A wheel loader that’s too wide might block foot traffic in urban sites. A generator that drinks diesel like water might wreck your sustainability goals.
Real-time modeling
Use BIM or 3D simulations to map equipment access, turning radii, lifting capabilities, and load distribution. Better yet, explore virtual environments where mistakes cost nothing. Platforms like TradeFox let workers and planners explore how machinery behaves, without endangering lives or wasting time on site.
What To Look For When Choosing Construction Equipment
Every construction project has its unique demands. But there’s a short list of equipment traits that should always align with design intent:
- Physical size and access: Will the equipment physically fit where it needs to go?
- Fuel consumption: Is it efficient enough for long days without frequent refueling?
- Reach and load limits: Can it handle the job’s vertical and horizontal demands?
- Mobility and terrain compatibility: Wheels or tracks? Smooth asphalt or muddy inclines?
- Power source: Diesel, electric, hybrid? Think about your environmental impact.
- Service and support availability: You can’t wait three weeks for parts mid-project.
- Operator interface: Will it enhance operator comfort and reduce fatigue over long shifts?
Choosing from a wide range of options might feel overwhelming, but filtering choices through the lens of design clears things up fast.
Digital Tools Bridging The Gap

Technology has quietly become the unsung hero of construction management. We’re no longer guessing what fits. We can test, iterate, and plan with digital twins and real-time simulations.
BIM: Building it Before You Build It
BIM lets you test the clash points between design and machinery. It’s not just for architects; it’s just as useful for logistics and equipment placement.
Simulation platforms
From crane swing arcs to trench width for backhoes, you can now simulate almost every movement on the site. It’s a shift from reactive to predictive planning.
TradeFox, for example, offers a way for tradespeople and planners to simulate job site conditions, helping bridge gaps in both knowledge and planning.
It’s a smart layer between theory and fieldwork, especially when training new crew members or prepping for high-risk tasks.
When It All Comes Together
Let’s talk real-world impact.
Say you’re managing an urban mid-rise build with tight alleyway access. Instead of choosing a standard tower crane, the team goes for a mobile telescopic unit with a smaller footprint.
Why? Because the design team brought in operations early, and together they mapped a lift plan using BIM. Materials moved faster, residents complained less, and fuel savings stacked up. That’s improved efficiency with a design-first mindset.
Or consider a greenfield industrial site where heavy rains turn everything to sludge. The designer includes equipment-friendly access paths in the site plan. The gear runs smoothly, downtime drops, and you’re not constantly hauling equipment out of mud. The overall project timeline benefits.
These aren’t hypotheticals; they’re the kind of wins you get when equipment decisions aren’t divorced from design.
The Road Ahead
The construction industry is evolving. Tight timelines, sustainability targets, and rising operational costs mean we can’t afford mismatched tools anymore. Equipment isn’t just about horsepower and hydraulics. It’s part of the design DNA now.
Forward-thinking construction companies are already shifting their approach. They’re investing in cross-disciplinary planning, embracing digital tools, and recognizing that heavy equipment plays a critical role not just in building, but in how the design unfolds.
Synergy isn’t a buzzword. It’s your buffer against inefficiency, rework, and blown budgets.
Final Word
Next time you’re sketching out the blueprint for a build, take a beat. Ask: What gear do we need? Better yet, ask: What gear fits the design, the site, and the crew?
Because when product & design move in lockstep, your job site becomes less of a guessing game and more of a well-oiled machine. Literally.